Facade Recladding: The Rebirth of 95 Wellington Street with Bethel White Granite Ventilated Facade
Facades and facade cladding systems serve as more than mere protective skins for buildings; they are dynamic interfaces with the environment, crucial for defining aesthetic identities and enhancing urban landscapes. These elements harness the power of design, technology, and material science, allowing for the creation of durable, energy-efficient exteriors that manage light, heat, and acoustics to augment occupant comfort and minimize environmental impact.
With sustainability at the forefront, the contemporary facades of buildings like 95 Wellington in Toronto are a testament to the ingenious integration of form and function. This architectural gem, part of the Toronto Dominion Centre and previously distinguished by an outdated aesthetic, has undergone a significant facelift. Its natural stone cladding with BETHEL WHITE™ granite has been meticulously planned and executed, respecting the original architectural vision while presenting a fresh, contemporary facade.
The Architectural Evolution of 95 Wellington
The Toronto-Dominion Centre complex, which celebrated its 50th anniversary in 2017, heralded a new era in Toronto’s skyline with its stark matte-black steel I-beams and floor-to-ceiling windows—hallmarks of Ludwig Mies van der Rohe’s trailblazing International Style. In its inception, the Centre broke the mold of traditional design, towering above the city’s masonry counterparts and marking a departure from the ornate facades of neighboring bank buildings. The vision for this urban transformation was shared by Allen Lambert, TD Bank’s visionary leader, and Fairview Corporation, now known as Cadillac Fairview.
Adjacent to the original towers designed by Mies van der Rohe stands 95 Wellington West, a later addition to the complex by Pellow + Associates, which demonstrates an architectural dialogue between its own unique style and the modernist aesthetics of its neighbors. In the 1980s, 95 Wellington Street West donned an exterior of rose-colored granite, a material choice that encapsulated the design trends of the time. As years passed, the facade system began to reveal the inevitable signs of aging, prompting discussions about a renovation that would address both its outdated appearance and underlying structural issues.
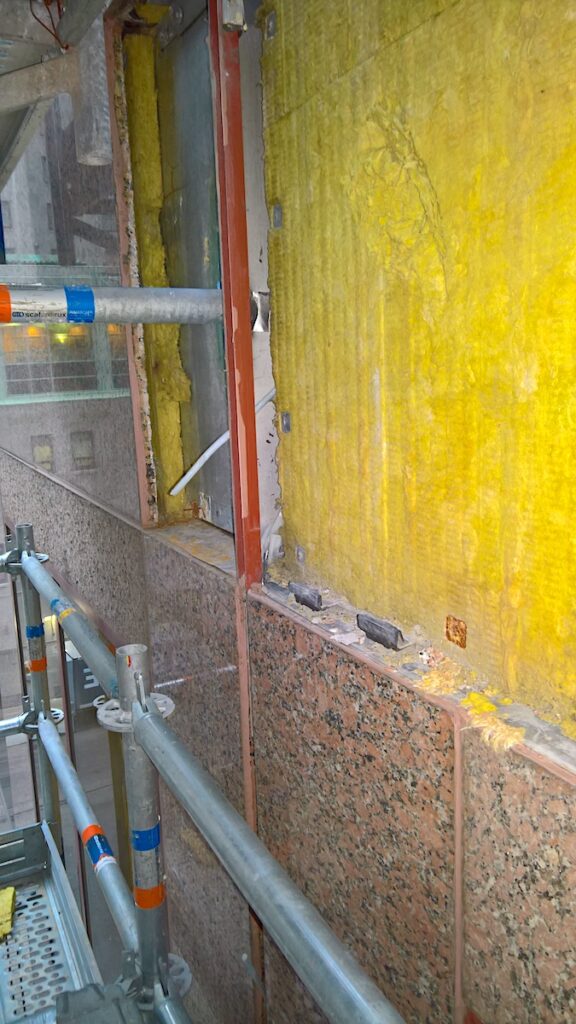

The original stone-faced steel truss panels on the building ran floor to ceiling and were connected back to the structure with stainless steel bent T-plate dovetails and galvanized bolts. Over time the galvanized bolts began to show signs of corrosion and started to snap.
Joe Scully, director of Eclad Stone Cladding Systems, provided insight into the original construction, noting, “The existing Texas Rose granite panels on the trusses were 4cm thick. There was nothing wrong with the stone but it was the anchoring system, and more specifically the bolts that were the issue,” he said. “But Cadillac Fairview wanted to give it a facelift and upgrade the stone specification so that is when we started looking at it with Polycor,” he concluded.
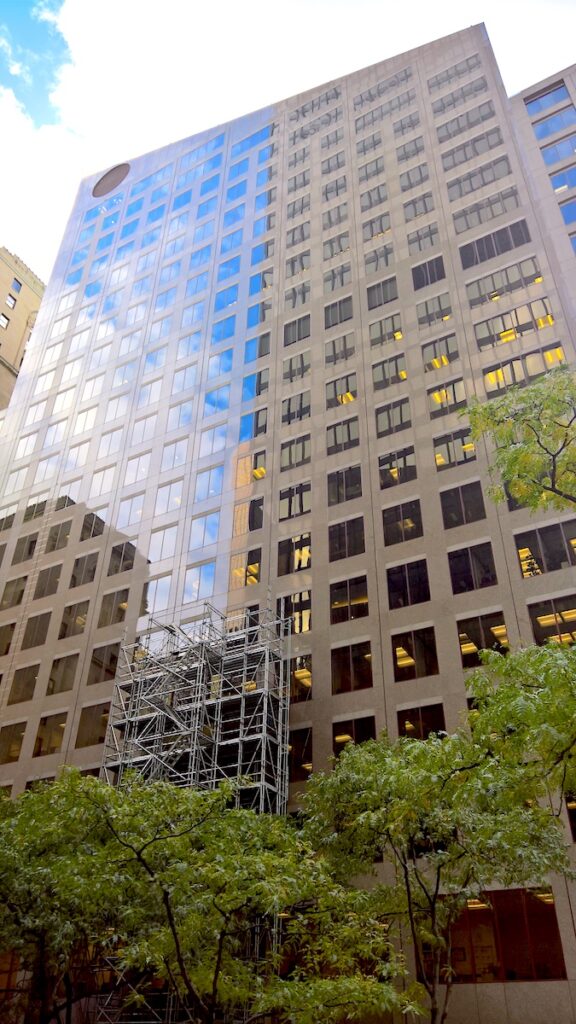

In the 1980s, when installing two steel truss panels together, they were not butted up tightly to each other. “The standard procedure was to leave wide expansion joints so there was a 1 inch gap between the panels on this particular building,” Scully said. He went on to describe how those gaps were managed in the existing system. “The gaps were filled with u-shaped, decorative aluminum channels that were not mechanically attached to the stone panels or the building, but instead held in place with silicone adhesive only,” he said.
The channels had begun to loosen over time and some joints were covered with tape to help seal the gaps and hold them in place out of an abundance of caution. The cavity behind the stone was also very minimal at only 7cm depth which did not allow for much insulation but the owner wanted to incorporate more than was originally installed. “This required some ingenuity to determine how to gain the several extra centimeters to allow for the added insulation,” Scully pointed out.
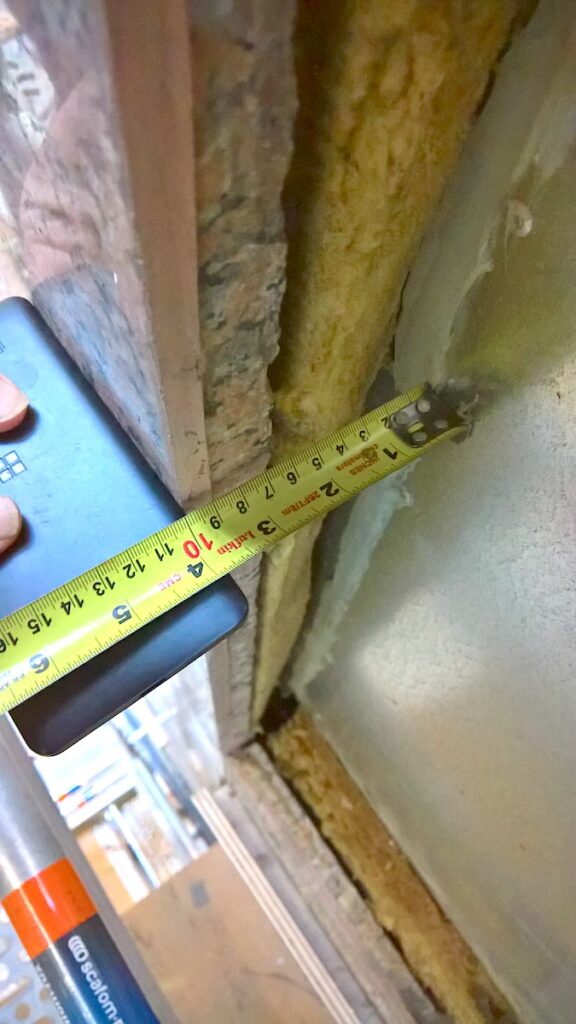
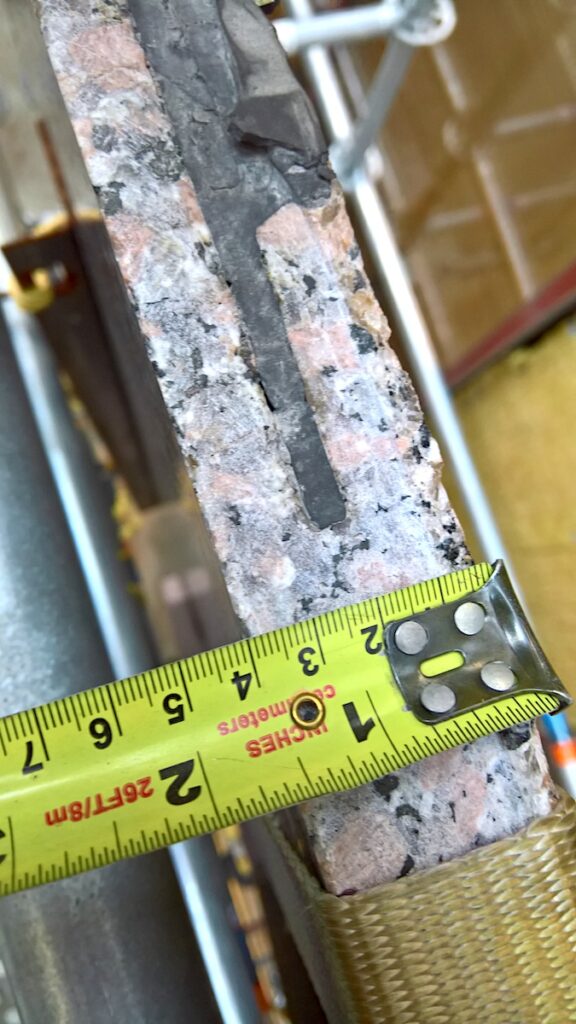
The Ingenuity Behind the Cladding: Eclad Anchoring System
The comprehensive upgrade of the cladding, air and vapor barriers, and insulation at 95 Wellington Street underscores the innovative use of the Eclad anchoring system. Chosen for its reliability and efficiency, the system was pivotal in facilitating a swifter and less labor-intensive installation process. Its aluminum grid structure, consisting of vertical and horizontal members, was bolted directly onto the existing structure, adeptly accommodating nearly all pre-existing variances with minimal disruption.
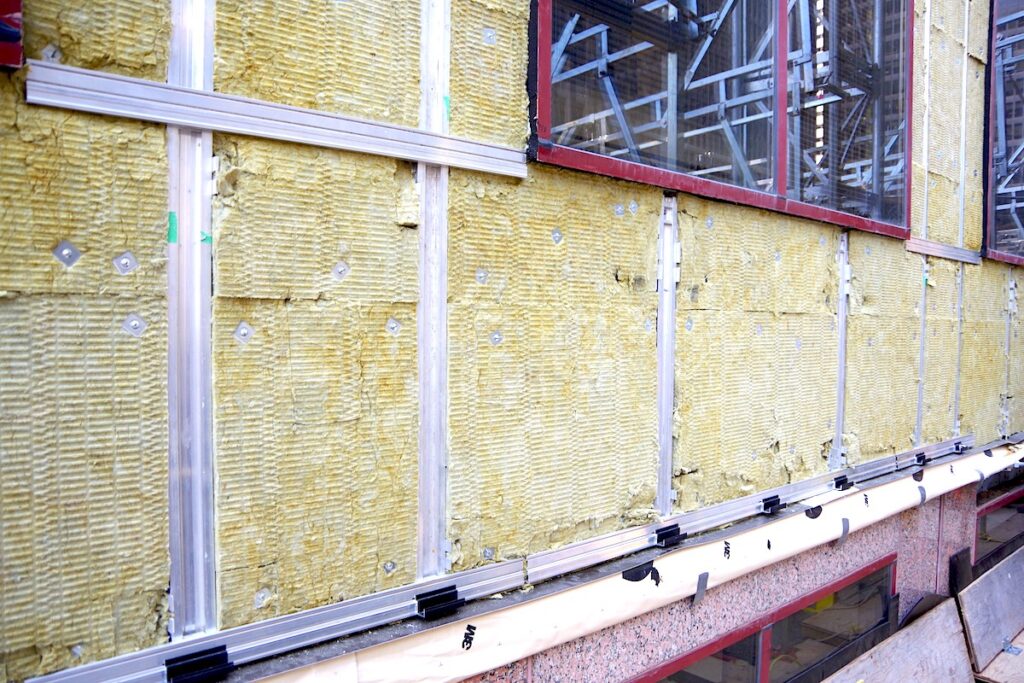
“Since this building was failing, the owners didn’t want to be guinea pigs on another system that didn’t have a track record,” shared Scully. ”They said they wanted a system that’s tried, tested and proved,” he said.
Since the cavity was not deep enough the decision was made to add caps to the existing windows, serving as extensions to gain the extra 2cm of space needed to beef up the insulation for a total of 9cm. “Customization lies at the heart of the Eclad system as evidenced in this project,” Scully said. “The standard 2×2 mullions wouldn’t fit on this retrofit due to the cavity size tolerances so we redeveloped them and made them thinner while still maintaining all the slide tracks and bars that are used to allow for thermal expansion and building movement,” he explained.
Two layers of Rockwool semi-rigid mineral wool were installed into the deeper wall cavity on top of 3M wrap adhered to the galvanized panels attached to the steel trusses.

The logistical strategies implemented in this project were as crucial as the materials and systems used. With the building remaining occupied and space at a premium, the project utilized mast climbers to remove the old cladding and transport the new wall panels, negating the need for swing stages and allowing for the undisturbed operation of the building.
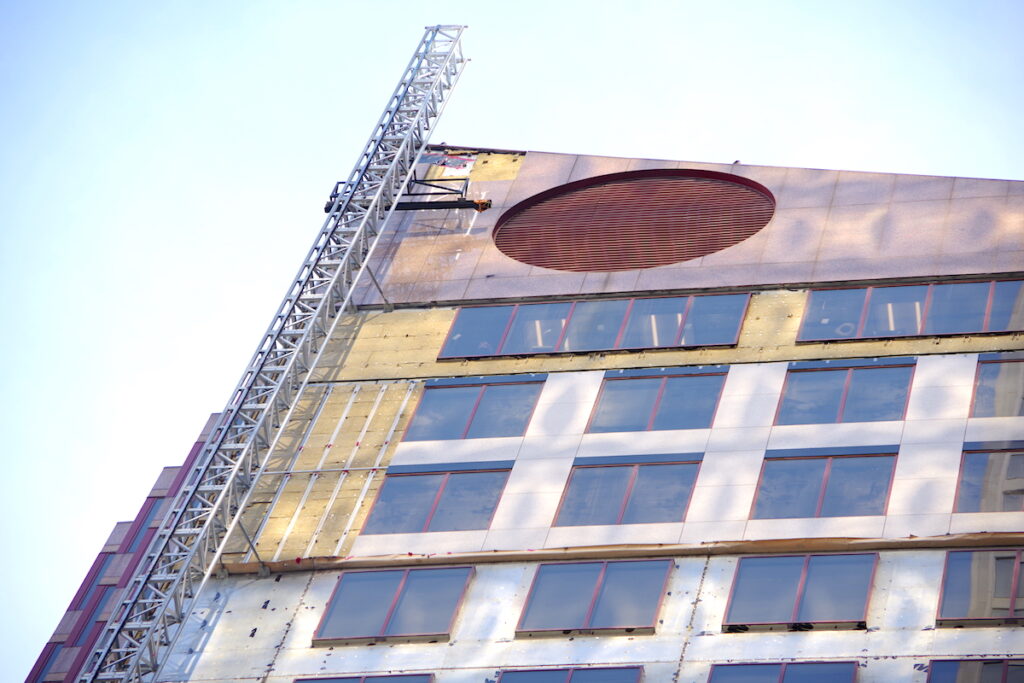
“The advantage of the system is you can work from the top down,” Scully pointed out. One of the main challenges was the building being 100% operational so it had to remain open during construction. “Because it was a living building with people still working on the inside, you can strip two to three floors at a time and then put the Eclad in,” he said. “The only time there would be any noise is when you are drilling into the steel structure, but after that, there is no noise since the stone just snaps in.” Heavy construction noise needed to be performed after hours, so the Eclad system assisted in maintaining productivity levels during the project. “There aren’t many systems out there where you can start working from the top down, leave areas out, and come back and put them in afterward,” Scully noted.
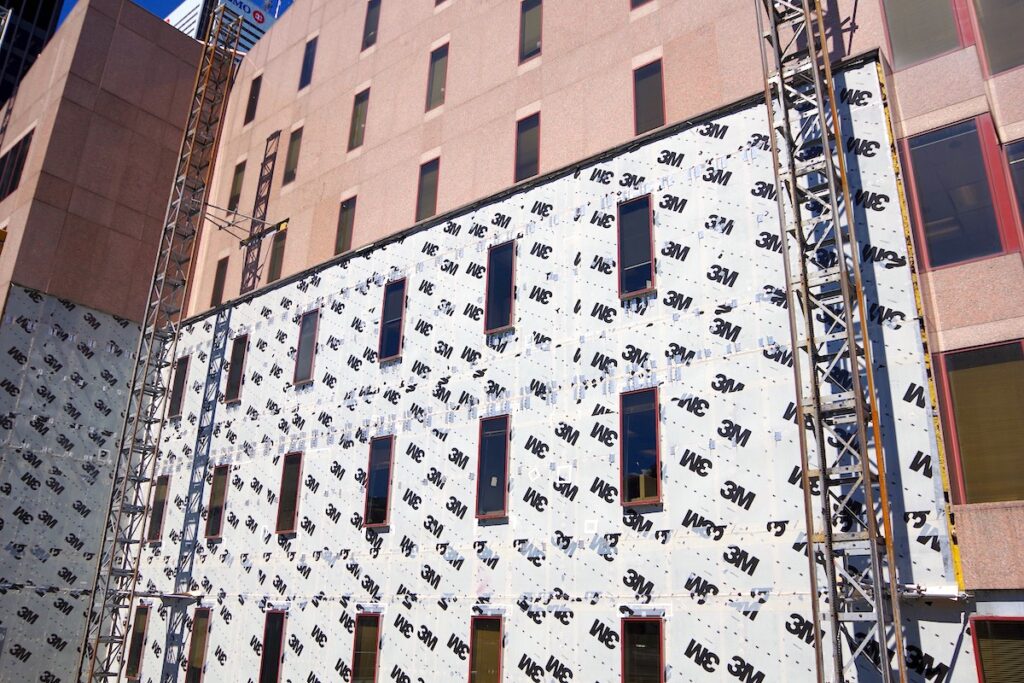
The Eclad system also serves as a ventilated rainscreen, an essential feature that ensures the structural wall remains dry. This open design allows air to circulate, diverting any penetrating moisture through the system’s channels, thus preserving the load-bearing wall’s integrity. Versatile in application, the Eclad system offers three variants to adapt to various surface materials, making it suitable for large-scale architectural projects, whether it be new constructions, retrofits, or restorations. The result of this meticulous process is not just a visually striking façade but one that exemplifies modern architectural ingenuity in its approach to preservation and sustainability.
A Timeless Material for a Modern Facade
The selection of Bethel White granite for the exterior reclad stands as a testament to both elegance and endurance. This granite is unique with its flawless, even grain and pure color, but it also sets the benchmark in the industry being the gold standard that all other white granites are measured by. The ADNOC building in Abu Dhabi, the Grande Arch in Paris, and the Smithsonian Museum in Washington D.C. are also clad in Bethel White granite.
Bethel White granite exterior wall cladding panels also carry the distinction of sustainability, certified by the Natural Stone Institute (NSI-373), and renowned for its resistance to oxidation—a quality that ensures its pristine white hue endures the test of time and exposure to the elements, never developing any rust spots.

This stone wall cladding selection is not only a nod to the building’s prestige but also a bold counterpoint to the dark hues of its architectural companions, particularly the iconic black steel of the neighboring Mies Van Der Rohe towers.
Vincent Roy, architectural sales manager at Polycor, remarked, “They wanted to make quite a statement with regards to the other buildings in the area that are all pitch black. So they said, ‘Well, why don’t we do a nice, white reclad.’”

Roy added, “They were very adamant at finding the whitest stone possible with the least amount of movement or shade variance inside, so there were quite a few slab reviews and mock-ups required which Polycor provided.”
Three stones were being proposed – 1 Spanish stone and 2 Canadian granites (Bethel White and Stanstead Grey™). “They went through all the testing of the stone, sampling, and follow-up meetings and got the stone specified then everything went out for the design – build – assist phase,” Roy said. “They were very adamant about the pull-out strength, modulus of rupture and flexual strength of the stone,” he pointed out. Both proposals from Polycor were suitable but the Spanish stone required an increased thickness for the panel sizes specified, coupled with the tight tolerances in the spec and the ASTM stone data. The Canadian granite performed better, allowing for a thinner 3cm panel.
For mock ups, slab inspections were first done at Polycor’s facility in Rivière-à-Pierre, then the cut-to-size stone was produced for the full-scale mock-ups and shipped to York Marble who performed the stone installation. Once the stone was secured, it was important to the architects and the GC that they perform their due diligence and visit the Bethel White quarry to validate the size, production and capabilities at the site. Roy accompanied them to the quarry and toured them through the operations in Bethel, Vermont.
Joe Scully added, “There was a time they were considering engineered stone or metal panels, but after learning that the color of those products could fade over time, and the proven track record of natural stone, they ultimately decided against it.”
The result is a harmonious contrast, a fresh and crisp appearance that breathes new life into the city’s skyline. The Bethel White granite cladding encapsulates the collective efforts of WZMH, PCL Construction, EXP, Entuitive, H.H. Angus & Associates Ltd., among others, to meld the historical significance of 95 Wellington with contemporary design principles, ensuring the building’s legacy for decades to come.
The Legacy and Future of 95 Wellington
By integrating natural stone into architectural projects, developers not only tap into the aesthetic and durable qualities of the material but also contribute positively to sustainability goals. Such use of natural stone can also help projects earn LEED credits, further reinforcing its position as a material of choice for those looking to marry construction needs with ecological responsibility. The utilization of locally sourced natural stone like Bethel White granite in the revitalization of 95 Wellington is a case study of how cladding system innovations and sustainable practices can be seamlessly woven into urban development, delivering benefits that extend beyond the immediate scope of the building itself. This blend of old and new is a tribute to the TD Centre’s importance to Toronto’s architectural narrative—a narrative of pioneering spirit and enduring influence.
Want to learn more about Polycor natural stone facades and how they are specified for various building types? Read more in the Museum Reinhard Ernst case study….
